AN EMERGING LEGENDSTM SERIES PRODUCT
environmentally friendly plating process
As part of our Emerging Legends™ series of new products and services, Cooper is excited to introduce electrolytic hard iron plating as the engineering standard for the protection and restoration of power cylinders for large compression and power generation engines. Concern for environment, health and safety is rendering the process of hexavalent chrome plating a less attractive option within gas compression industry. Accordingly, the hard iron plating process replaces the use of porous chrome plating in its entirety within Cooper. Electrolytic hard iron plating has been used for many years and has a successful track record as an alternative to porous chrome plating.
Hard iron plating is available for large bore power cylinder repair on most engine product lines, including Clark, Cooper-Bessemer, Enterprise, Ingersoll Rand, and Worthington.

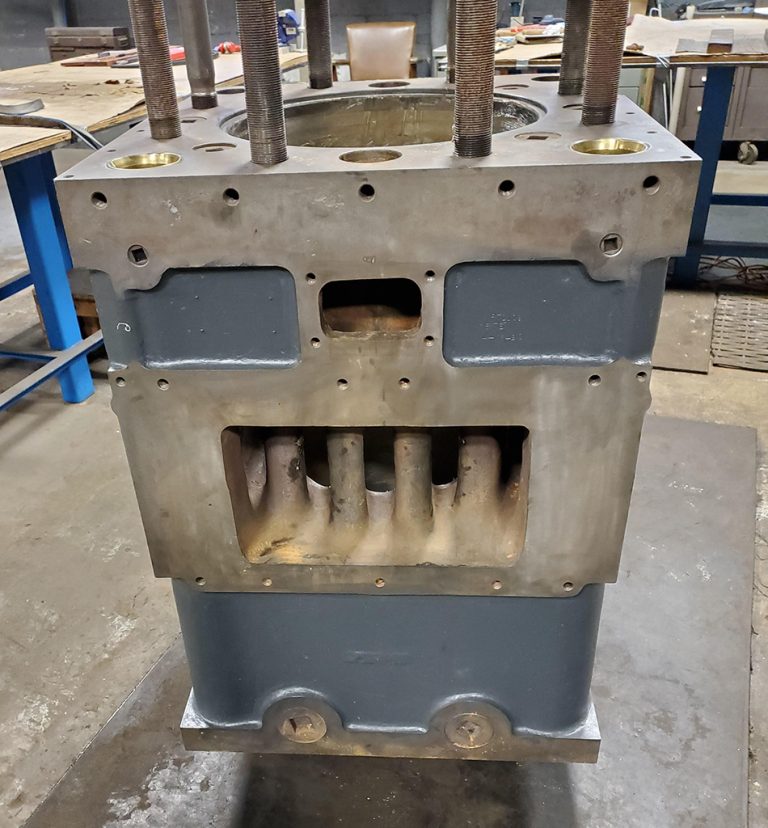

Hard Iron Plating in place of
chrome plating
The hard iron plating process was developed as an alternative to chrome plating for cylinder reclamation with a low environmental impact. Hard iron plating is 99.9% pure electrodeposited iron with excellent adhesion properties and can be molecularly bonded to a wide range of base metals. It is applied in the same manner as chrome plating and can be inspected under identical technical guidelines for adhesion and porosity variation.
Hard iron plating has the appearance of an original cast iron cylinder. It has an average tensile strength of 235,000 psi and sheer strength exceeding 50,000 psi. The average hardness of hard iron plating is 45-50 HRc (421 Brinell). The hardest portion of the deposit is typically an average of 0.008 inch thick nearest the outer surface.
The hard iron plating cell can accommodate most major lines of power cylinders including the gas compression industry’s largest such as the Cooper Bessemer Z-330 20” cylinders and the Clark, Ingersoll Rand, and Worthington 17” cylinders, or any smaller sizes.
Cooper’s hard iron plating is also superior to thermally sprayed coatings for power cylinder restoration as our product has no limitations for material bonding and ring compatibility. Furthermore, restoration with sprayed coatings is limited to 0.050” of thickness, whereas the restoration can be much greater with hard iron plating.
Key advantages
- Environmentally Friendly
Hard iron plating is 99.9% pure electrodeposited iron with physical properties comparable to low carbon steel. If the chemicals used in the hard iron plating process are neutralized and packaged correctly, they can be disposed of as a class III non-hazardous waste.
- Outstanding Porosity
One of the most important and beneficial features of electrolytic hard iron plating is the porosity of the surface. Here, the term porosity refers to “pores” in the surface of the cylinder that act as lubricating oil reservoirs. The porosity is mechanically induced by honing.
- Sour Gas Fit
An additional benefit of hard iron plating over chrome plating is its suitability for sour gas applications. Chrome plating does not hold up well when the H2S levels exceed 1% in the fuel. Hard iron plating has become the standard coating for cylinders in all engines using fuels with more than 1% H2S.
- Parts Commonality
For the end user, the transition from chrome plating to electrolytic hard iron plating is seamless. Both hard iron and chrome cylinders can be used in the same engine at the same time. The same power ring sets are used for both.

Cooper’s new electrolytic hard iron plating for power cylinders is an inaugural member of the Emerging Legends™ Series, our portfolio of new products and services that advance the industry and transform Cooper’s traditional way of doing business. Emerging Legends™ serves as a testament to the Cooper commitment of optimizing performance of legacy engines and compressors, helping our customers extend the life of their equipment, and bringing environmentally sustainable solutions to the market.
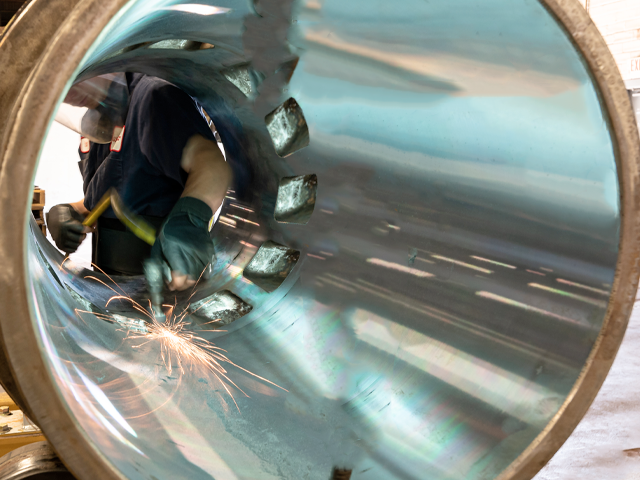
Manufacturing Facility
Cooper’s center-of-excellence (COE) for hard iron plating in Houston, Texas specializes in the repair of large bore power parts for reciprocating engines. The state-of-the-art 4,870 sq.ft. hard iron plating manufacturing cell houses equipment such as a stripping tank, multiple plating tanks, hot-water and cold-water tanks, wax tank, magnesium sulphate tank, rectifier and circulating pumps. The repair process consists of stripping, vertical turning lathe (VTL) for boring, honing, plating, grinding, VTL for finish bore, final honing, cleaning, and inspection. Each cylinder or liner is 100% inspected for straightness, concentricity, and roundness. After passing inspection, the cylinders are hydrotested at 100 psi and 180°F. Finally, the cylinders are packaged and crated for shipment.
Contact your Cooper sales representative to learn more about our electrolytic hard iron plating capabilities.