UPGRADE OFFERING
CLEANBURN PLUSTM uPGRADe
Reduces methane output by up to 40%
The reduction of greenhouse gases, particularly methane, is a key element of Cooper’s emissions reduction technology offering. To improve the environmental impact of engine-compressors operating within our industry, Cooper is pleased to announce CleanBurn Plus™, an emission reduction solution tailored to reduce fuel consumption, fuel slip, methane leakage, and unburned hydrocarbons.
Cooper’s CleanBurn Plus™ upgrade package is a comprehensive solution that can reduce methane output by up to 40% in most of the industry’s integral engine-compressors. For a fleet of engines rated collectively at 100,000 HP, this level of CO2e reduction can equal 20,000 tons/year, equivalent to the elimination of 4,348 standard passenger cars.
Our CleanBurn Plus™ upgrades are offered across our entire integral engine-compressor product line to include AJAX®, Cooper-Bessemer®, Clark, Enterprise®, Ingersoll Rand, Superior®, and Worthington.
Product | |||||||
---|---|---|---|---|---|---|---|
Cooper-Bessemer | |||||||
Worthington | |||||||
Cooper-Bessemer | |||||||
Clark | |||||||
Worthington | |||||||
Ingersoll Rand | |||||||
Ingersoll Rand | |||||||
Cooper-Bessemer | |||||||
Cooper-Bessemer | |||||||
Clark | |||||||
Worthington | |||||||
Clark | |||||||
Ingersoll Rand | |||||||
AJAX |
* Based on 4,500 operating hours/year, 930BTU/ft3 fuel
** Average passenger car generates 4.60 Tonnes CO2e/year (U.S. EPA)
*** 1 Bbl crude oil generates 0.43 Tonnes CO2e (U.S. EPA)
**** Average U.S. home generates 8.30 Tonnes CO2e/year (U.S. EPA)
CUSTOMIZING UPGRADES BASED ON YOUR INDIVIDUAL NEEDS
SOLUTIONS for ENGINE & COMPRESSOR UPGRADES
For decades, Cooper has been providing technology and engineering services for upgrades for all makes and models of integral and separable engines and compressors. With our advanced technologies, expertise, and project management experience, we offer upgrades to reduce engine emissions, increase horsepower, improve efficiencies and reliability of your equipment, and reduce maintenance costs. Cooper has the products and expertise to upgrade your engine or compressor and meet or exceed the emissions and performance levels you need. Upgrades include, but are not limited to, jet cell conversions, air/fuel ratio improvements, blower/turbocharger upgrades, ignition system upgrades, and electronic control panels.
To further strengthen our upgrade portfolio, Cooper acquired HOERBIGER’s Engines Services (HES) division in 2019. Cooper now offers even more upgrade technologies, including the HyperFuel System™, HyperBalance™, HyperLogic™, ePCC™, and ePFI™. The Engine Services team offers engine emissions reduction and efficiency improvement upgrades, applicable to all types of engines such as slow-speed, high-speed, 2-stroke, and 4-stroke. To date, Engine Services has applied more than 350 engine upgrades to nearly every type of gas compression engine currently in existence.
0.5 g/bhp-hr NOx SOLUTION UPGRADES
Cooper’s acquisition of HOERBIGER’s Engine Solutions division has allowed us to become the market leader once again in offering upgrades for your engine automation and emissions reduction. Cooper is very proud to offer a complete engine upgrade solution for 0.5 g/bhp-hr NOx emission that is available for all Clark, Cooper-Bessemer, and Ingersoll Rand slow-speed engine models. This solution has been implemented on numerous engines in field operation and is fully backed by Cooper’s guarantee.
Contacts
Vice President, Engineering
Hans Mathews
Mobile | +1 (713) 962-7161 |
[email protected] |
VP, Sales & Marketing
Patrick Gillespie
Mobile | +1 (832) 316-9506 |
[email protected] |
Major Engine Upgrades
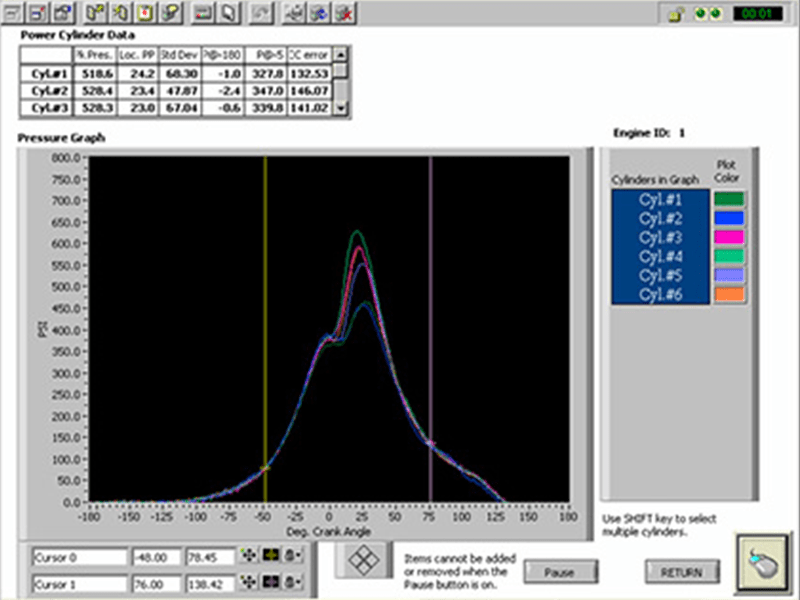

HyperBalance IV™ Upgrades

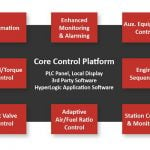
HyperLogic™ Upgrades
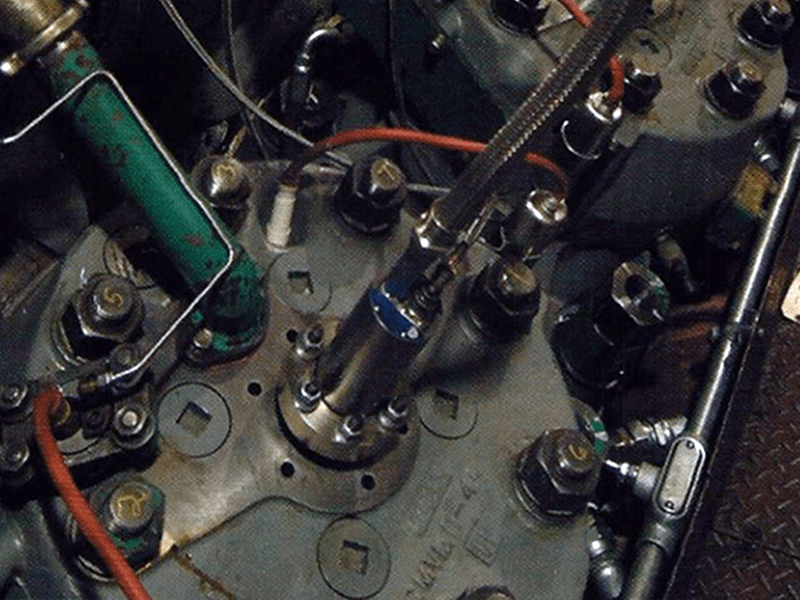

HyperFuel™ System Upgrades


EFC™ (Electronic Fuel Control System) Upgrades


Electronic Port Fuel Injector System (ePFI)
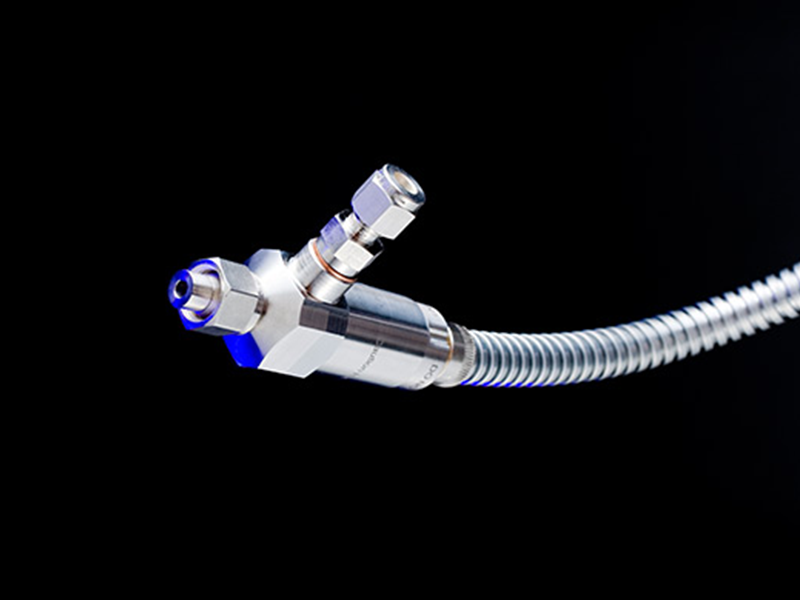

Electronic Pre-Combustion Chamber (ePCC)
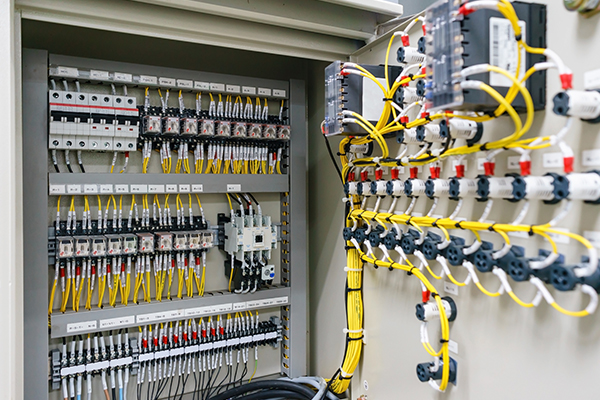

Control Panel Upgrades
Upgrade List by Product Lines
To learn about all available upgrades for your assets, click on the link below for each product line.
Cooper Machinery Services and its products and services are not sponsored, authorized, or endorsed by Caterpillar, Clark, Ingersoll Rand, Waukesha, or Worthington. All non-O.E.M. product names are property of their respective owners. Any references to trademarked names are solely for informational purposes and do not constitute a claim of ownership by Cooper Machinery Services of CAT, Clark, Ingersoll Rand, Waukesha, or Worthington. CAT is a registered trademark of Caterpillar, Inc. Waukesha is a registered trademark of INNIO Waukesha Gas Engines, Inc. Ingersoll Rand is a registered trademark of Ingersoll Rand, Inc.”