field service is the lifeblood of cooper
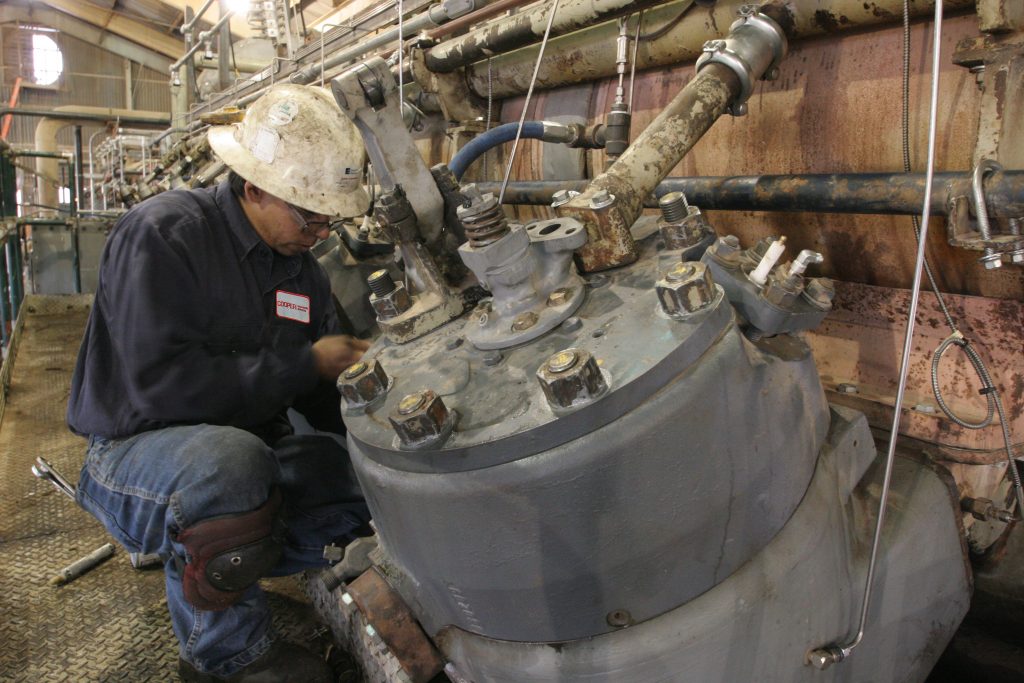
Our field service personnel are on the front lines with our customers each and every day. That is why Cooper spends so much time ensuring our service representatives and technicians are highly trained, sensitive to the customer needs, and always prepared to provide quality and quick global response — anytime, anywhere.
At Cooper, we pride ourselves on servicing most makes and models of high-speed and slow-speed engines and compressors including AJAX®, CAT, Clark, Cooper-Bessemer®, Enterprise®, Gemini®, Ingersoll Rand, Superior®, Waukesha, and Worthington. We also repair and upgrade a large line of engine turbochargers including ABB, Caterpillar, Clark, Cooper®, Delaval, and Elliott®. With a product line so broad, it’s a top priority of Cooper that we employ and train only the finest service personnel in the industry for Engine and Compressor Services.
Field Services
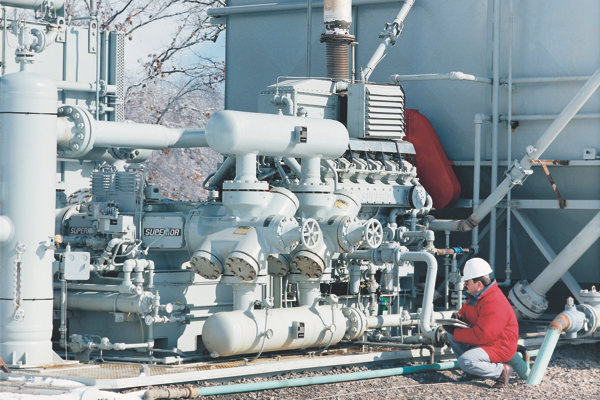
Cooper understands that our customers’ equipment is critical to maintaining the operation of gas gathering and gas transmission pipelines. Our experienced technicians can inspect your equipment and provide needed preventative maintenance to keep it running, lessening the likelihood of breakdowns.
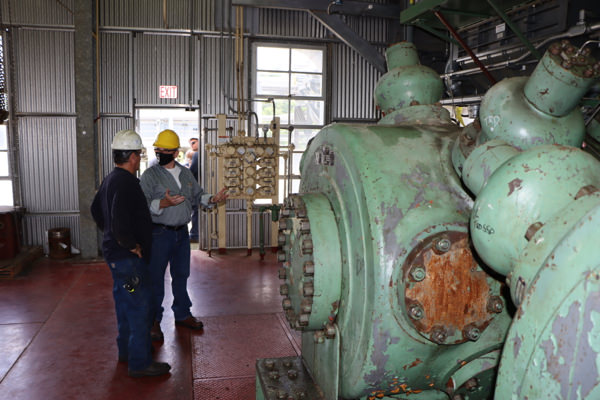
From smaller jobs to larger projects, we are here to serve you. Call on Cooper for equipment relocation and reapplication, engineered solutions, predictive emissions monitoring, alignment services, grout services, compressor resizing, and contract maintenance. We provide retrofit services to enhance engine performance and meet new emission requirements.
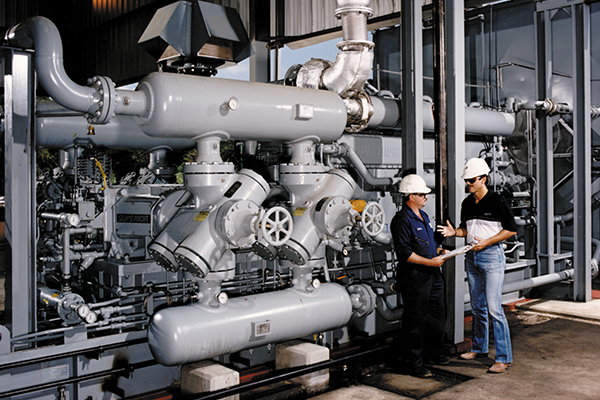
Experienced and highly skilled service representatives from Cooper are available worldwide to assist with equipment installation and commissioning. Cooper provides training at the customer’s location or online to help them with the smooth operation of their equipment. Training aims to maximize equipment efficiency and build life-long skills for your personnel.
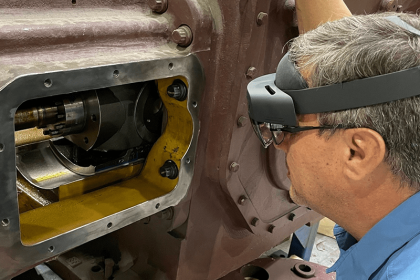
Introducing the Microsoft HoloLens 2, a self-contained holographic headset that allows field service personnel to use video conferencing and mixed reality while working “hands-free.” Field workers can share real-time views of the engine-compressor problem while remotely working with one of Cooper’s 50+ engineers from our technical team who can diagnose and troubleshoot. Launched in Q2, 2022, the new HoloLens system is just another revolutionary way Cooper is changing the compression industry for the better.
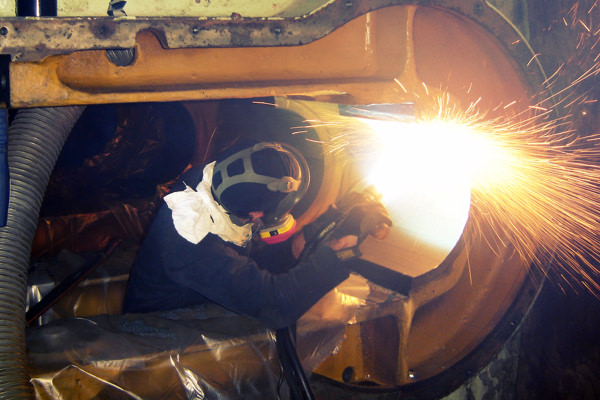
Contact: Daryl Roberts (903) 267-0241
When time and wear take their toll on hard-working gas compression equipment, it is sometimes necessary to re-machine key parts so they can, once again, perform at their peak efficiency. Cooper’s field machining services save time and money by providing a cost-effective alternative to equipment removal. Our experienced service technicians can perform multiple machining tasks onsite including base and frame laser alignment, wireline, line bore machining, metal spray, compressor liner replacement, and more.
Field Machining Capabilities
- Line bore main bearings on engine and compressor frames
- Wire lining to determine if bores are misaligned
- Metal-spraying bores to restore to O.E.M. sizes, including clipping and spraying of the caps
- Machine/sleeve power cylinder bores on engines
- Boring diameters oversize to receive oversized liners, if required
- Boring diameters oversize to receive inserts to bring bores back to O.E.M. dimensions
- Re-line compressor cylinders
- Machining the bore oversize to receive oversize piston and wear bands
- Boring the liner out, if applicable, and installing a new liner
- Flange-facing and machining flat surfaces
- Crankshafts, flywheels
- Compressor cylinder end faces
- Engine top decks
- Reclaim register fits on various components
- Gear boxes
- Blower housings
- Ream holes
- Remove broken bolts, studs
- Metal-Lok crack repair
- Non-destructive testing
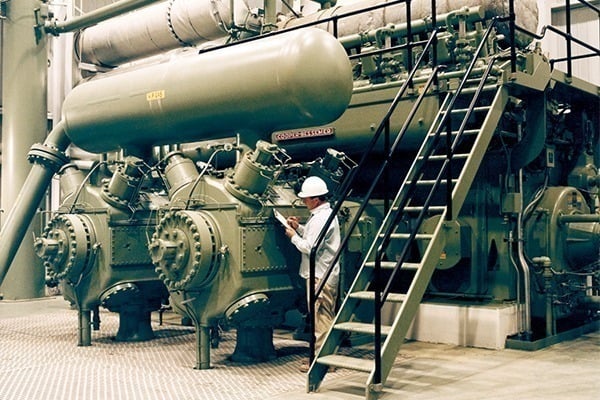
Cooper offers a variety of service agreements aimed at meeting the needs of our customers on a long-term basis. From regular maintenance agreements to total operation management, our service agreements are designed to meet a customer’s specific requirements, goals, and budget. Our commitment to optimum customer care ensures that you will always have the best possible plant availability, lowest possible operating costs, and the security of proactive planning for spare and replacement parts.
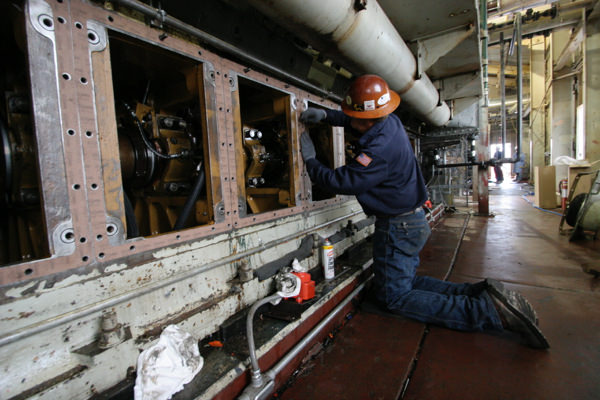
Service technicians are available for tear down, inspection, and rebuild of large integral and separable engines and compressors. New retrofits and safety upgrades can be installed to further improve operating efficiency during the overhaul. Advanced planning of an overhaul can lead to smoother execution and recommissioning.
Advanced Planning
- Up to one year ahead of time.
- Multiple reviews of overhaul scope, which eliminates omissions and errors.
- Identify and manufacture special order components.
- Pre-ordering of long lead items eliminates expediting charges.
- Overhauls executed as a single work stream utilizing the same crew from start to finish reduces delays or interruptions.
- Smoother overhaul execution and recommissioning.
Contacts
Vice President, Field Operations
Bernie McCoy
Mobile | 713-314-6926 |
[email protected] |
Field Service Manager
Greg Gonzales
Mobile | +1 (281) 770-1383 |
[email protected] |
Jason Merillat
Mobile | 720-810-7208 |
[email protected] |
Field Service Supervisors
Mark Chaffino – Deer Park, TX
Mobile | 832-358-5556 |
[email protected] |
Darryl Hill – Southeast Region
Mobile | 504-202-1276 |
[email protected] |
Berry Ingram – West Region
Mobile | 432-208-1929 |
[email protected] |
Steven Kirkpatrick – Northeast Region
Mobile | 606-225-6831 |
[email protected] |
Henry Verrett
Mobile | 985-860-4958 |
[email protected] |
Director, Technology
A.D. Szilagyi
Mobile | 832-655-7461 |
[email protected] |
experience, expertise, & exceptional service
We've been at this for a while
No one has been servicing compression and power equipment longer than Cooper. When an engine or compressor does not operate to its fullest rated capability, it is our reputation on the line. That’s why we place so much value on the training and expertise of our service personnel. They are, as we like to say, the lifeblood of our company. When you have a need for engine or compressor service, we are confident that our Cooper team will be there fast with a solution that fits your needs.
We work safely. We work efficiently. We work with common sense.
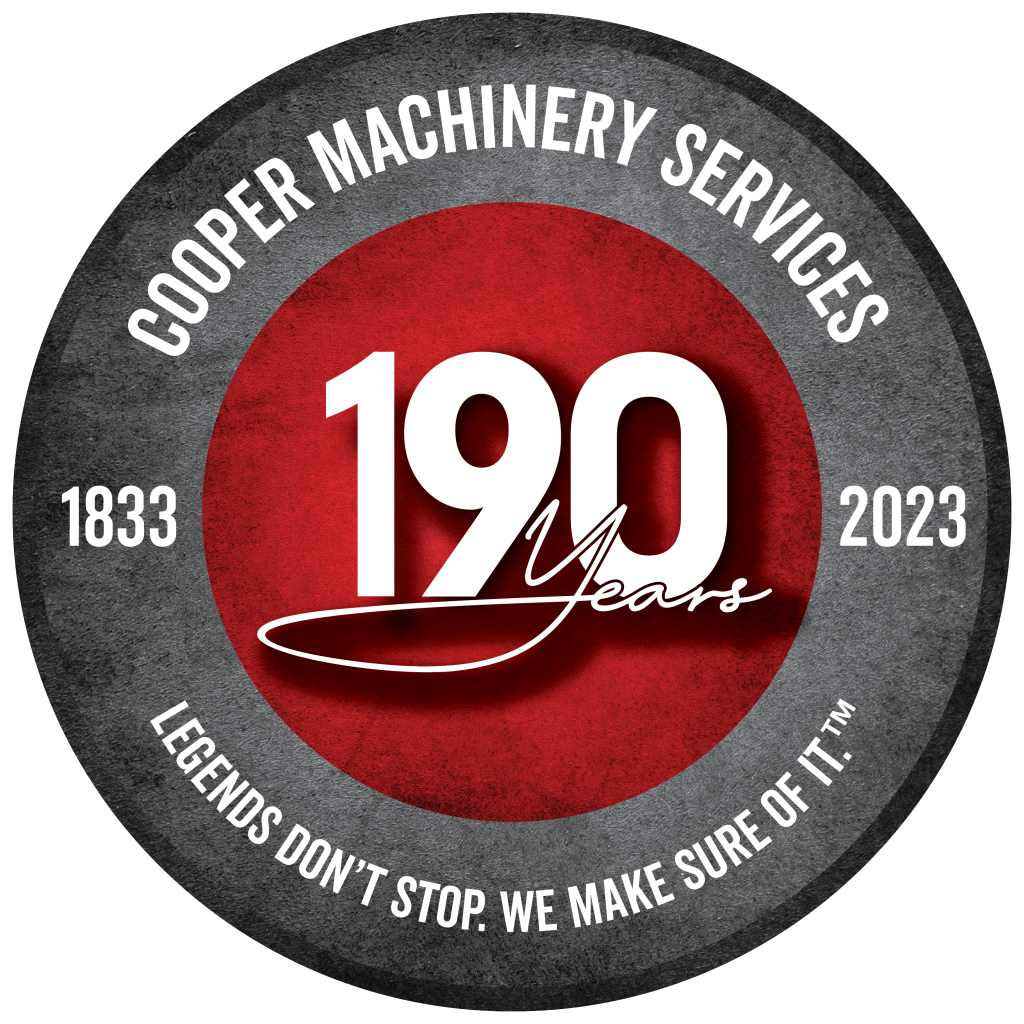
SATISFACTION GUARANTEED
customer Testimonial
“The Cooper crew that was sent out to do the overhaul did a great job in getting the work done. All
performed well and did a great job getting the unit overhauled. All three guys were very skilled, very
safety oriented, took and followed directions well. If at all possible, I would like to see them all come
back to do the overhaul on the next unit. I enjoyed working with these guys and am looking forward to
seeing them again.
Clark Station Superintendent, Northeast Region. June, 2020
Cooper Machinery Services and its products and services are not sponsored, authorized, or endorsed by Caterpillar, Clark, Ingersoll Rand, Waukesha, or Worthington. All non-O.E.M. product names are property of their respective owners. Any references to trademarked names are solely for informational purposes and do not constitute a claim of ownership by Cooper Machinery Services of CAT, Clark, Ingersoll Rand, Waukesha, or Worthington. CAT is a registered trademark of Caterpillar, Inc. Waukesha is a registered trademark of INNIO Waukesha Gas Engines, Inc. Ingersoll Rand is a registered trademark of Ingersoll Rand, Inc.”