OVERVIEW
Engine Misfire Detection
Engine fire problems may continue unnoticed and undiagnosed and lead to significance methane and hydrocarbon (HC) emissions in exhaust from the unburned fuel. Furthermore, it can also damage the catalytic converter if an aftertreatment has been deployed to reduce emissions. Cooper offers solutions for engine misfire detection.
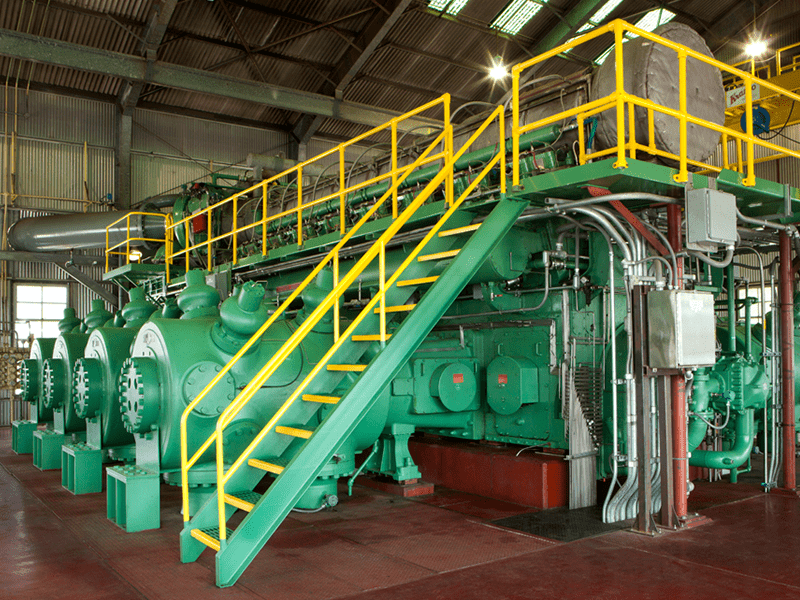

HyperBalance IVTM System
The HyperBalance IV uses pressure data from the pressure sensors to detect misfires or incomplete combustion. The misfires are tracked from time and a fault can be generated or shutdown can be initiated if the power cylinder is deemed to misfire consistently.
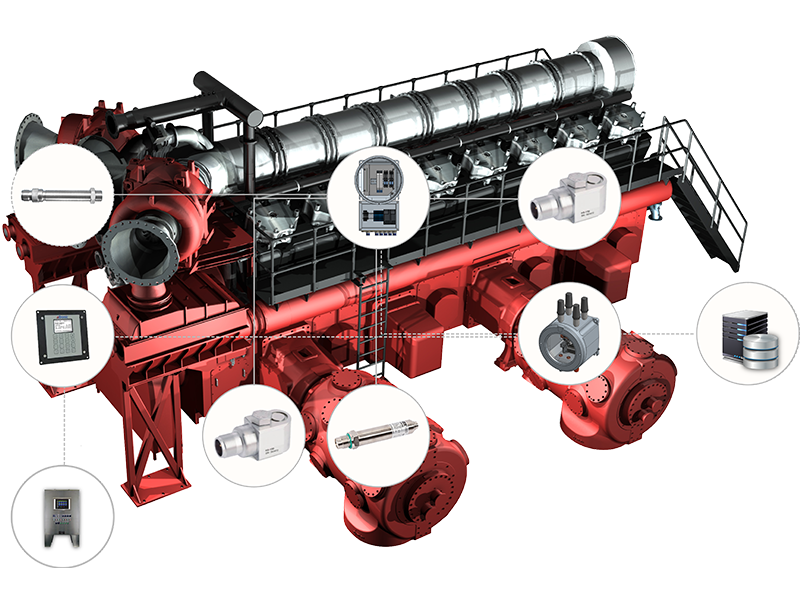
Cooper Performance Management System
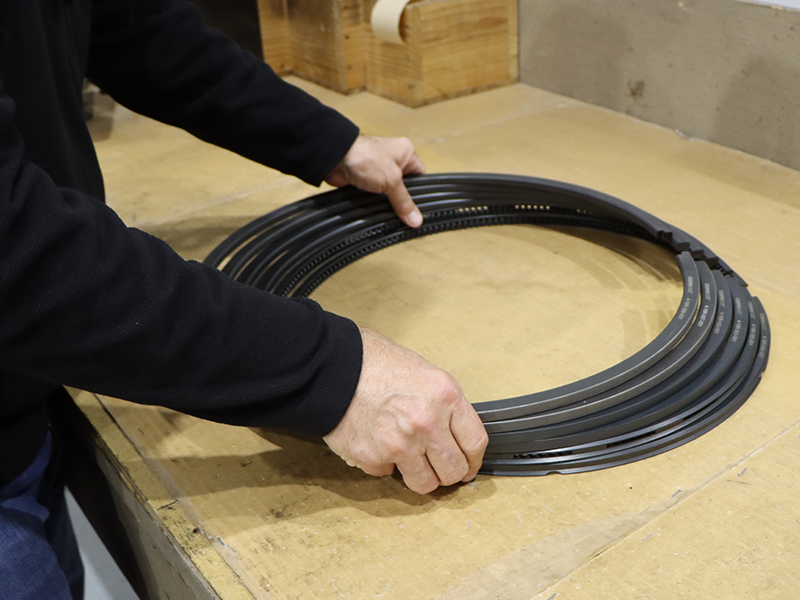
Extended Life Power Piston Rings
A primary function of the engine piston rings is to seal the combustion chamber from the crankcase. If excess combustion gases slip past the ring pack, they can enter the crank case and cause rapid deterioration of the crankcase lubricant. When these combustion gases escape the crank case they will bypass any exhaust gas treatment unless they are routed back to the intake manifold. Poorly sealing engine piston rings will eventually lower the compression ratio of the engine and reduce the fuel efficiency of the engine.
Piston rings will generally go through a break-in period where they slowly wear down the surface irregularities that allow a certain amount of combustion gases to slip past the rings. After the rings are properly broken-in they should normally function reliably for a long period. As the rings slowly wear out however, the end gap will grow, steadily increasing gas leakage and reducing the efficiency of the seal. When the leakage leads to unacceptable blow-by or poor fuel efficiency (and high oil consumption) the rings will have to be replaced.
By using Cooper’s Mo2 rings, thanks to the dual purpose coating, the break-in period will be much quicker and the long time wear rate will be slower leading to a better performing piston ring seal for a longer time compared to other types of piston ring coatings.
E.S.G. at Cooper
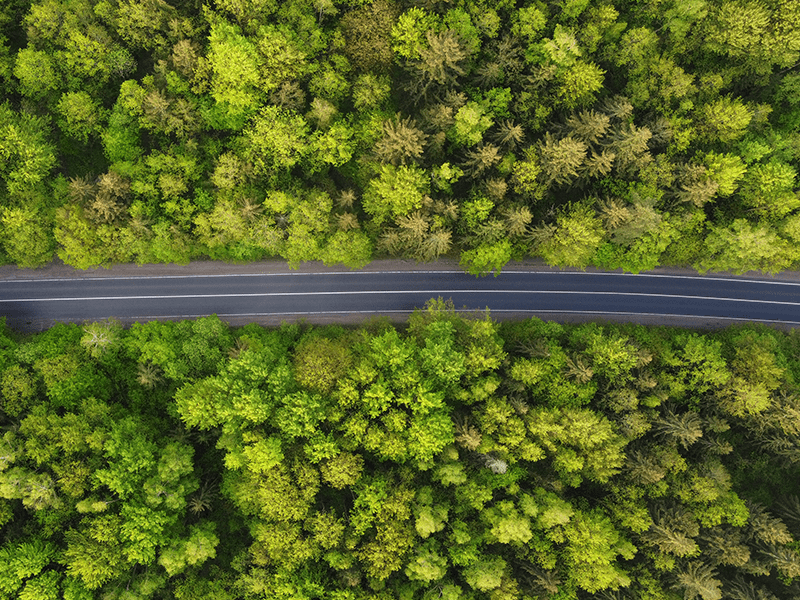
E.S.G. Journey
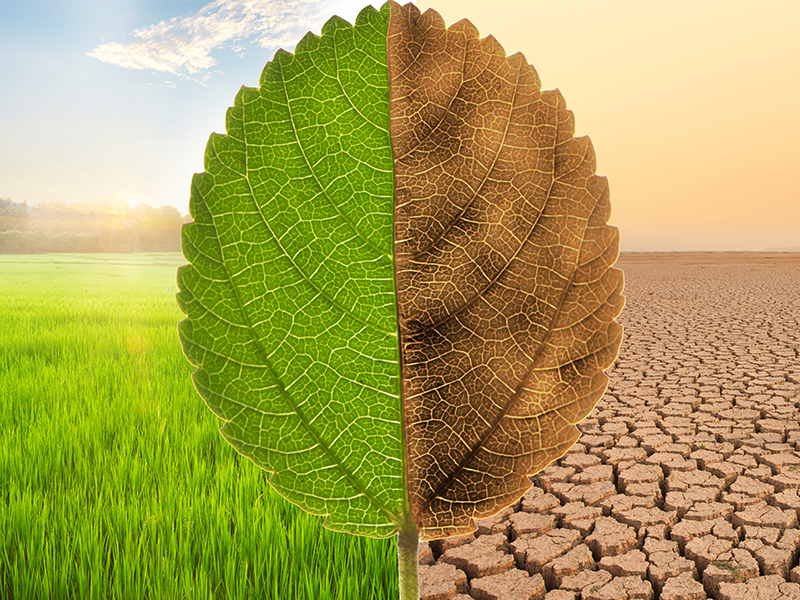
Environmental
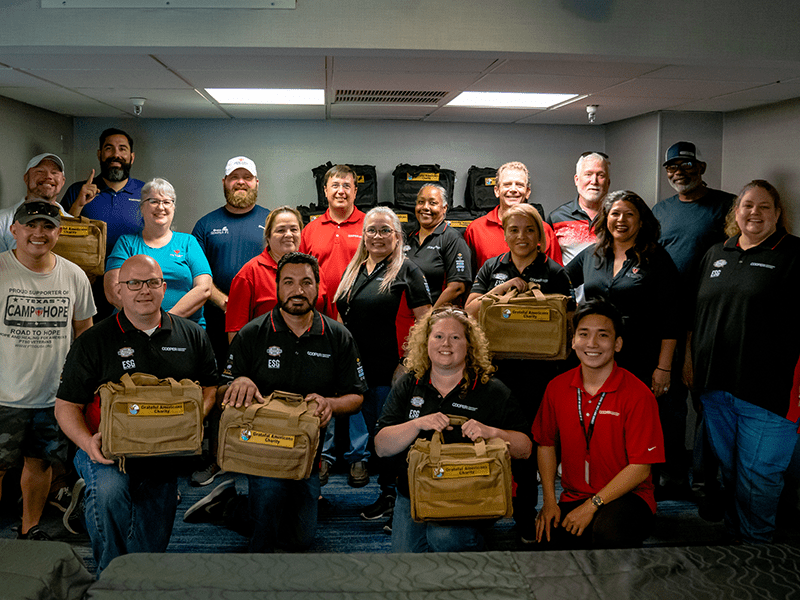
Social
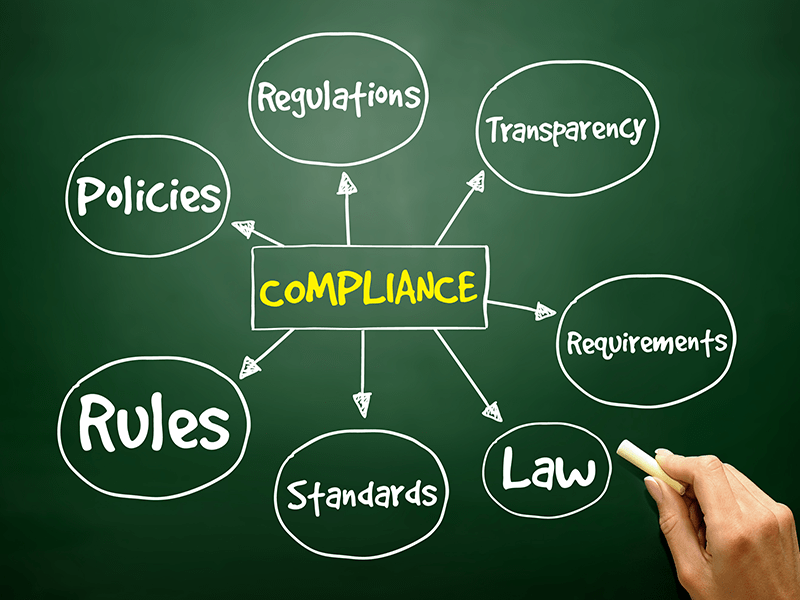
Governance
Helping Our Customers with their journey
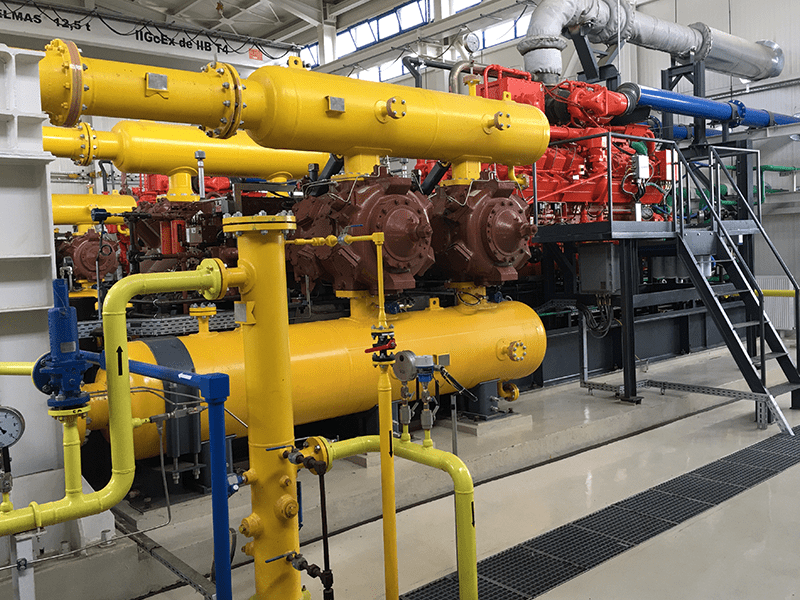
Hydrogen & Landfill Gases
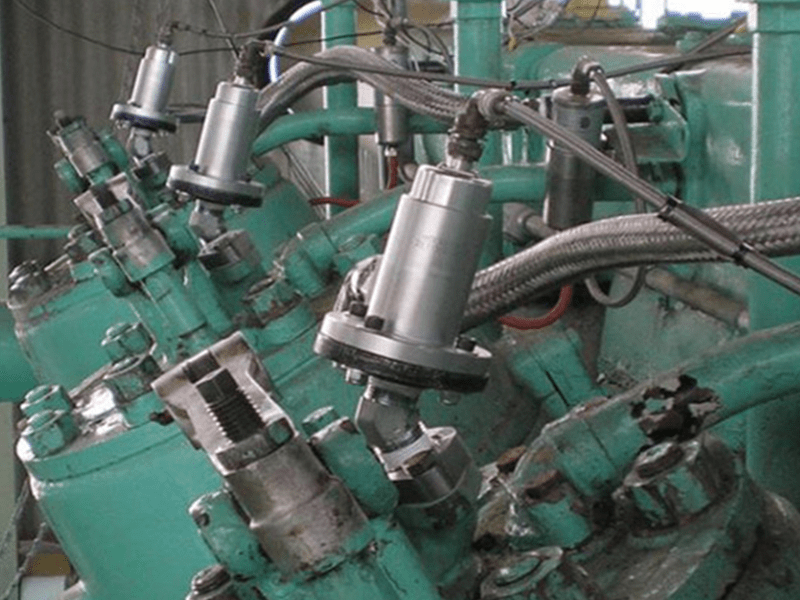
Equipment Upgrades
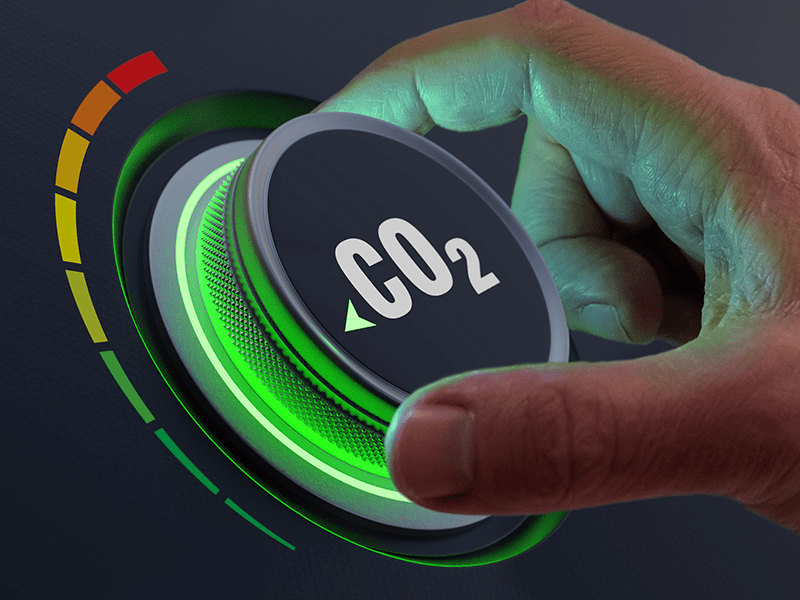
Operational Efficiency
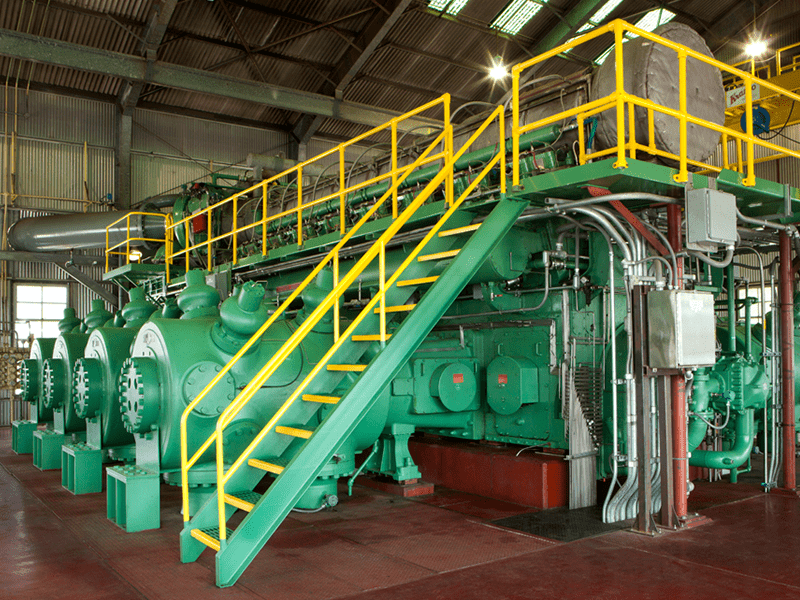
Unburned Fuel Emissions
& Exhaust Leaks
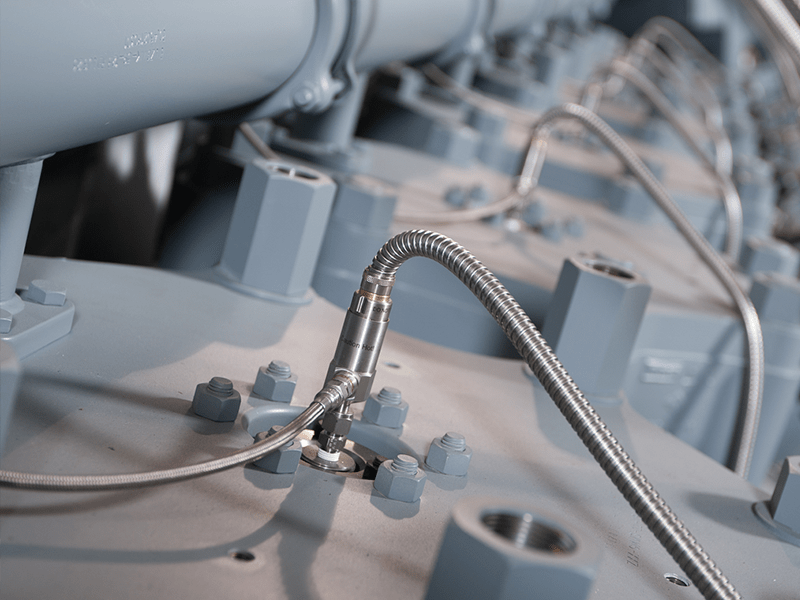
Emissions Reduction
DOWNLOADS
- Cooper Expands After-Sales Support Offerings | Gas Compression Magazine, August 2021 , Page 16
- Cooper Shifts ESG Push into High Gear | ESG Review, First Quarter 2022, Pages 10 – 13
- Hydrogen Natural Gas Fuel Blend Lowers Emissions for AJAX Integral Engine-Compressor | ESG Review, March 30, 2022
- Cooper Integral Engine-Compressor Burns 30% Hydrogen by Volume | Gas Compression Magazine, October 2022, Pages 32 and 34